2022年6月に開催された「日本ものづくりワールド」。 出展企業のひとつ、株式会社 八幡ねじは、終戦の翌年に、ねじの一種であるボルトの製造工場を立ち上げて以降、 多様なニーズに応え続け、事業を拡大。 “モノづくり” を “ねじづくり” で支え続ける取り組みの最先端を取材した。
▼進化を続ける“ねじづくり”の現在地
金属や木材など、様々なもの同士を「締結(部材と部材を結びつけて固定すること)」する“ねじ”。日本へは、火縄銃と共にポルトガルから伝来したと言われている。
その後、高度成長期には“産業の塩”と呼ばれるほど、日本のものづくりに欠かすことのできない部品となった。やがて技術の高度化や規格基準化が進み、産業としての体制が整備された歴史がある。現代においては、ねじに締結を超えた付加価値を生み出そうと、各社がしのぎを削っている。
今回、日本ものづくりワールドの機械要素技術展で展示をしていた、株式会社 八幡ねじは、終戦の翌年 1946年に創業。日本の再建と復興に寄与しようと、ねじの一種であるボルトの製造工場を立ち上げて以降、あらゆるニーズに応え続け、事業を拡大。創業76年を迎えた現在、取り扱い製品は約45万種類を超える。強みは、高機能製品の開発だ。製品自体の品質向上に加え、製造現場や社会、環境にも目を向け、あらゆる課題を解決しようと開発された商品が次々と誕生している。
▼長年の課題 ねじの〇〇〇を克服
まず紹介いただいたのは「くさびナット」という商品。
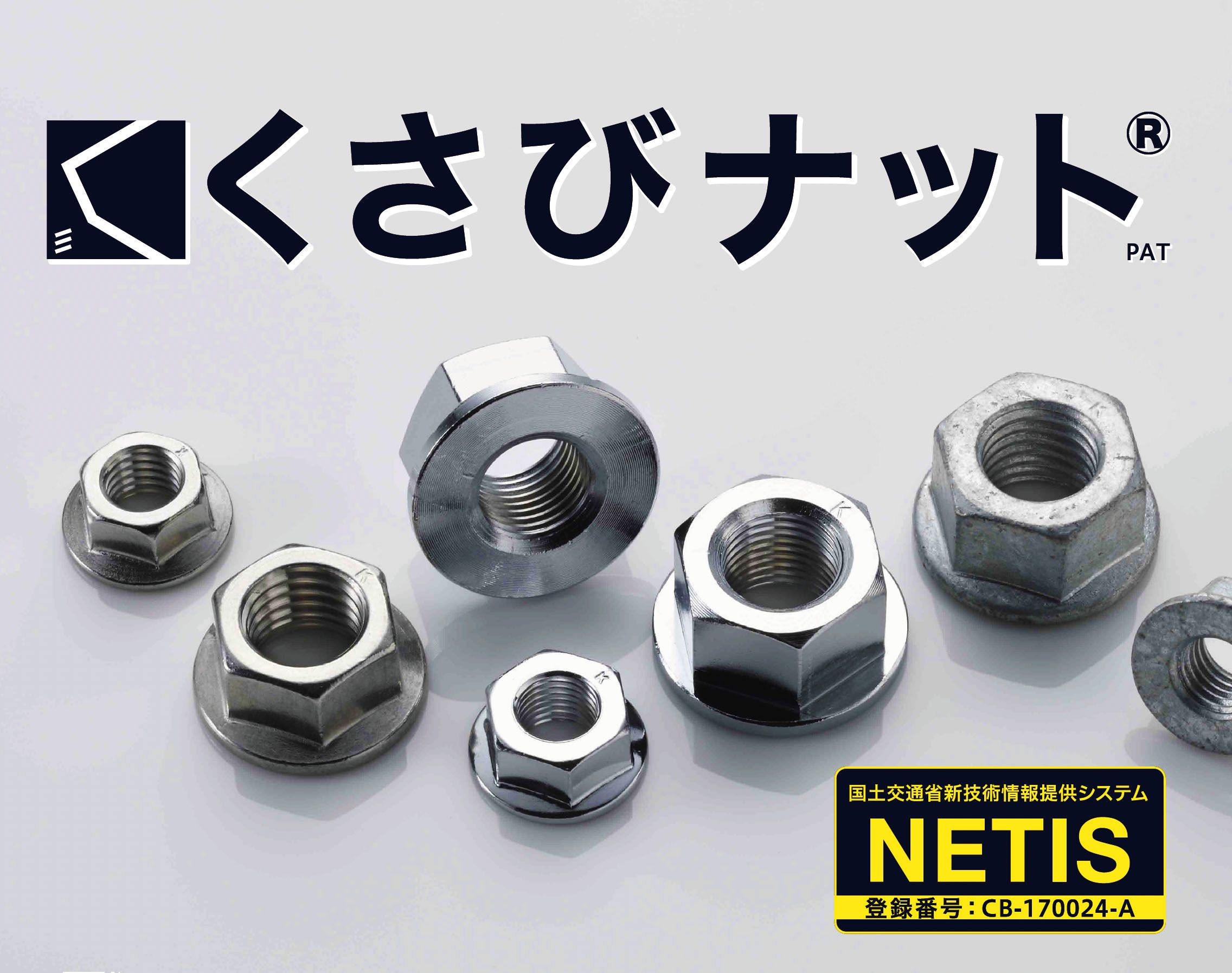
そもそも、ねじには大きく分けて「雄ねじ」と「雌ねじ」がある。ボルトなどの「雄ねじ」は外側に、ナットなどの「雌ねじ」は内側に溝が入っており、双方の対称的な溝を嚙み合わせ、締結することが多い。しかし、この「くさびナット」のねじ山はくさび型(谷が傾斜になっている形状)になっている。
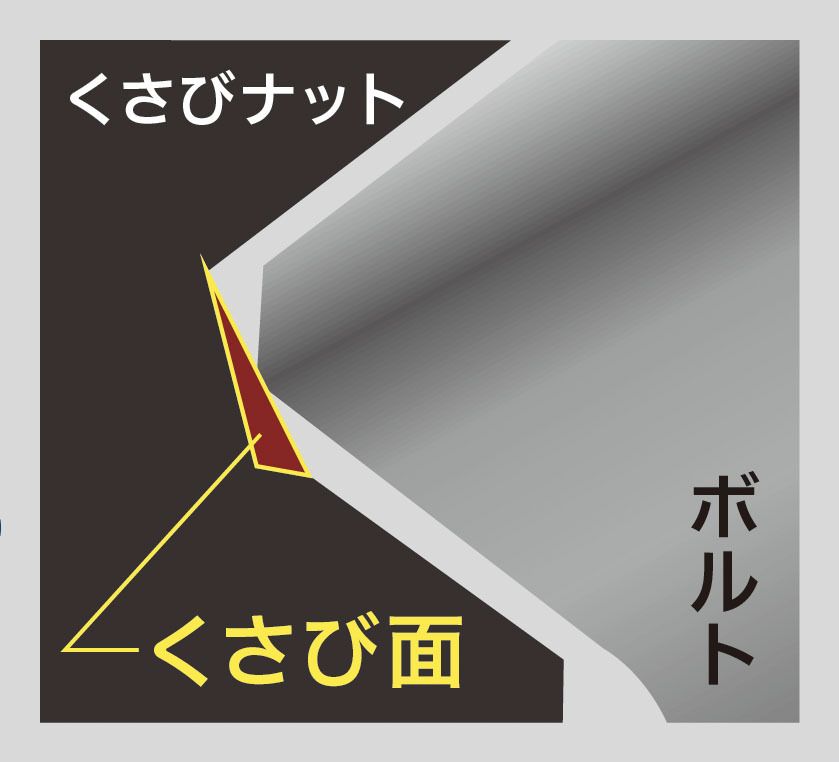
その理由は、ねじの長年の課題である“ゆるみ”を防止するためである。
一般的なボルトとナットの締結部を拡大してみると、部品の内部で働く力が一点に集中してしまっているのがわかる。激しい振動が加わると、一点だけでは耐えきれなくなり、結果的にゆるみが生じてしまう。
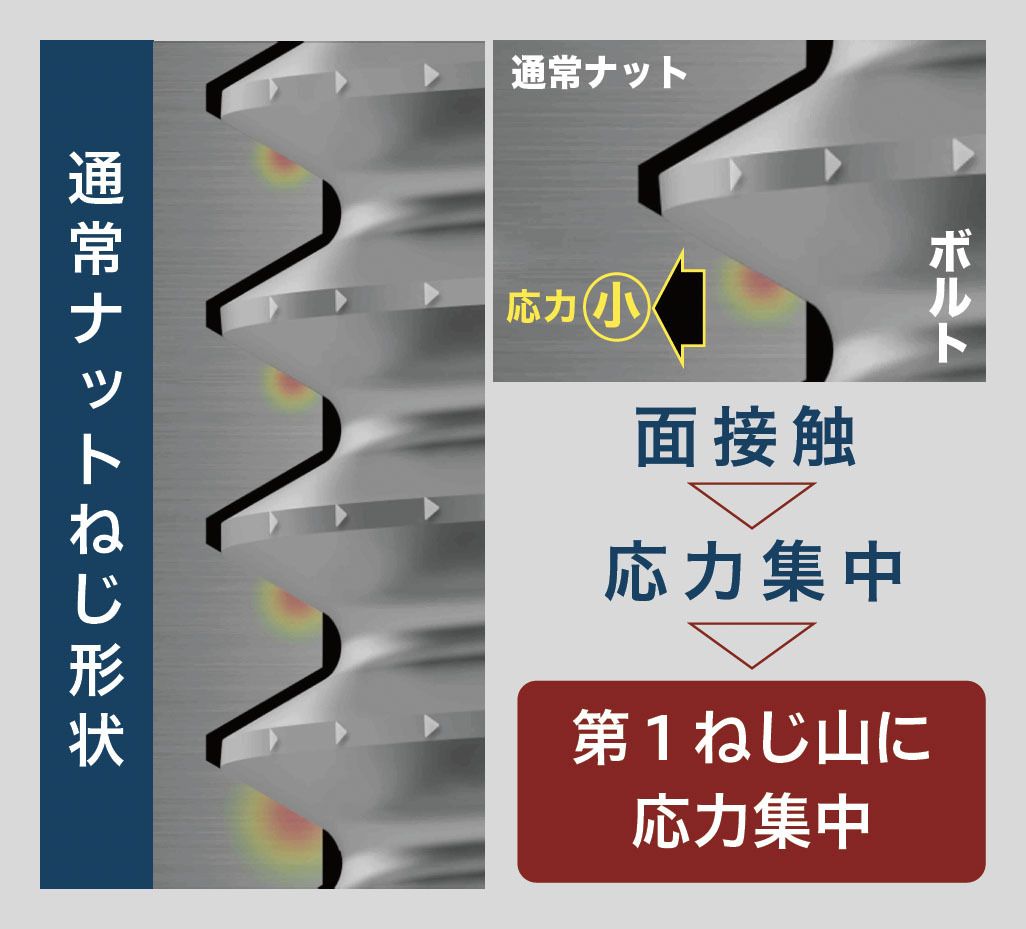
そこで、ねじ山の形状に着目し、一点に集中していた力を、部品全体に分散させる方法が研究された。その中で生まれたのが、ナットのねじ山をくさび型にする方法。従来よりも、ボルトとナットが接する面積が増え、力が分散しやすくなり、締結力の強化が実現した。
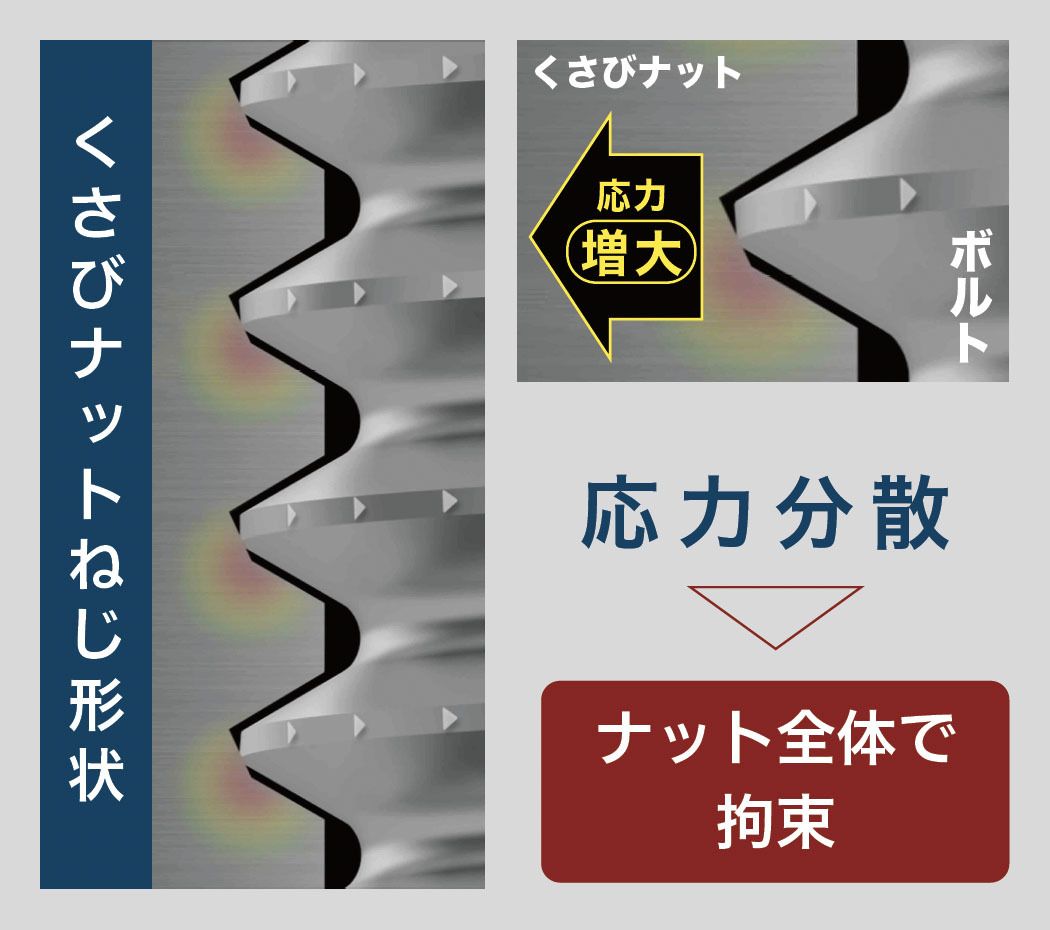
さらに、「くさびナット」は、強い締結力を持ちながらも、ねじを締め切るまでの作業を抵抗なく行うことができるため、現場の労力軽減にも繋がるそう。高所での作業など、力を込めるのが難しい環境での活用を提案しているそうだ。
▼機械の高精度・高品質化のために、ねじも進化
次に紹介いただいたのは「新型クリンチングスタッドボルト」だ。これまで販売されてきた「クリンチングスタッドボルト」の進化版である。「クリンチングスタッドボルト」は、専用の機械を使い、強い圧をかけることで、部品と部品を強力に締結でき、自動車部品の製造現場で使われることが多いボルトだ。
改善されたのは、締結時のバリ(出っ張り)の抑制。写真左側が従来品、右側が新製品である。

従来品は、締結時に部品内部に、写真のようなバリ(出っ張り)が生じることがある。
わずかなものにも思えるが、実際に触れてみると、ボルトの周辺が盛り上がっているのが分かる。精密機械の高精度・高品質化が求められる現代のモノづくり。小さなねじが、製品全体に与える影響は大きい。ミリ単位のバリであっても、機械の故障に繋がりかねず、解決が喫緊の課題となっているのだ。
一方で、写真右側の「“新型”クリンチングスタッドボルト」はバリを最小限に抑えている。秘密は、ボルトの頭部。内側に入った、星形のような溝にある。
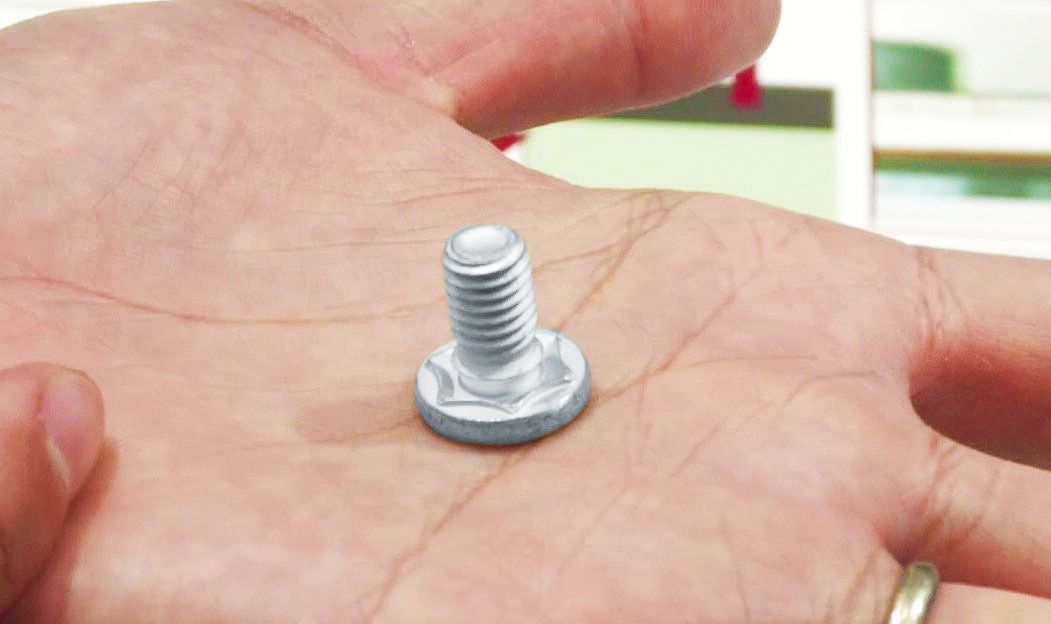
バリが生じる原因のひとつに、締結時にボルトに加わる強い圧がある。強い圧が、ボルトの頭部に加わることで、以下の写真のように、部品側の素材が押し込められ、行き場を失った素材が盛り上がり、バリとなってしまう。
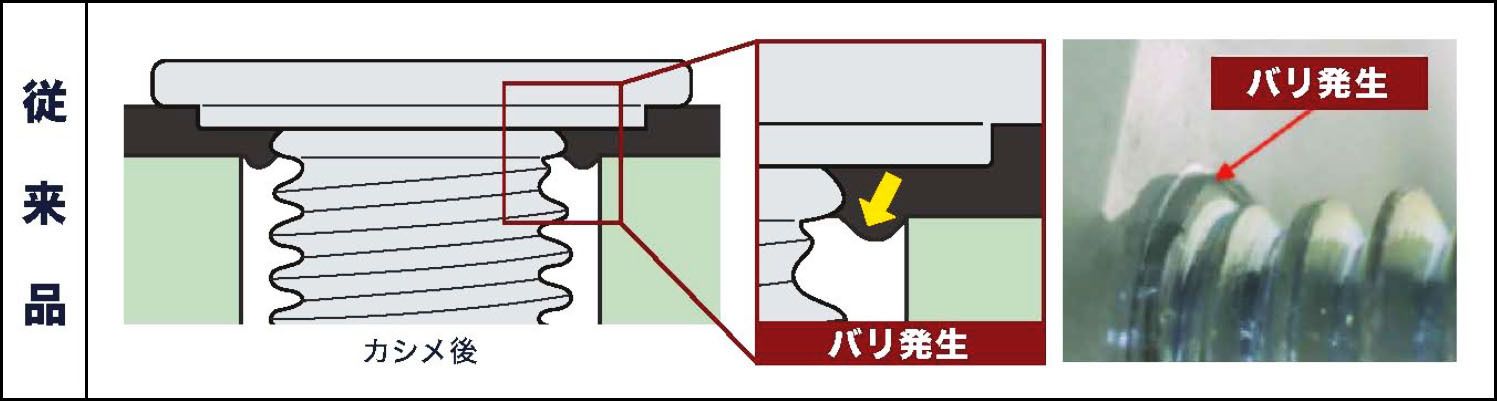
しかし、ねじに溝をつくることで、ボルト頭部からの圧によって、反対側に盛り上がってしまう素材の逃げ場をつくることができ、バリを軽減できる仕組みなのだ。わずかな溝であるが、この工夫により、バリを抑制することができる。
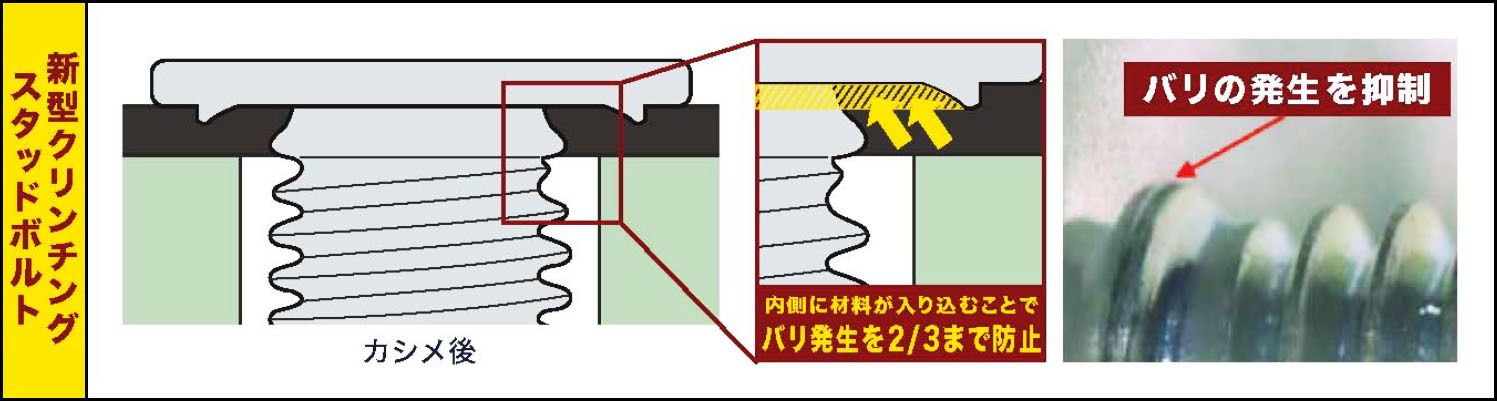
すでに多く活用されている自動車業界はもちろんのこと、家電・エネルギー業界に対しても活用の提案をしているそうだ。
▼環境に優しいモノづくりのために
製造現場だけでなく、環境に寄り添ったモノづくりも進んでいる。
水の力でアルミニウム部品を強化
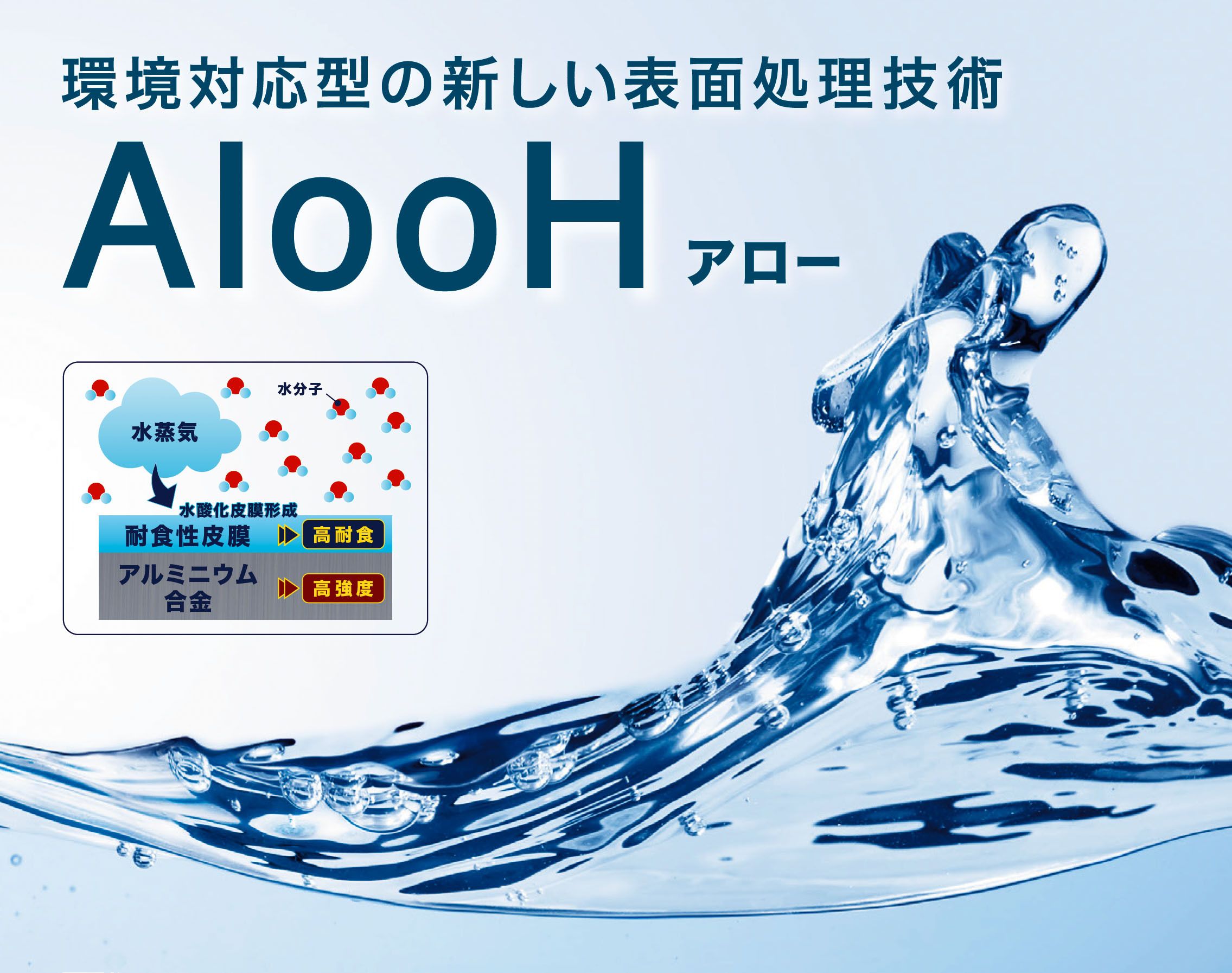
1つ目は、アルミニウム部品の表面処理技術「AlooH(アロー)」である。アルミニウムが、製造現場に欠かすことのできない素材である理由として、他の金属に比べて非常に軽く、加工もしやすいという優れた特性が挙げられる。一方で、空気中に含まれる酸素や水と反応しやすいために、サビなどの腐食の原因になりやすいのが難点でもある。
これらの弱点を補う方法として提案されていたのが「AlooH(アロー)」。アルミニウムの部品を専用の容器に入れて、高温・高圧下で水蒸気にさらすことで、部品の表面に、錆に強い膜が出来あがる。これにより、耐食性試験では、加工をしていないアルミ部品に1時間未満でサビが発生したのに対し、AlooHでは、8時間経過してもサビの発生は見られなかった。
アルミニウムの腐食を防ぐための加工方法には、環境負荷の大きい溶剤の使用が必要になったり、大量の電力を消費したりするものもあるが、「AlooH(アロー)」では水の力のみで、アルミニウム部品を錆から守ることができ、環境にも優しい。
さらに、部品を高温にさらすことで素材自体の強化も可能となった。
鉄の腐食対策技術も進化
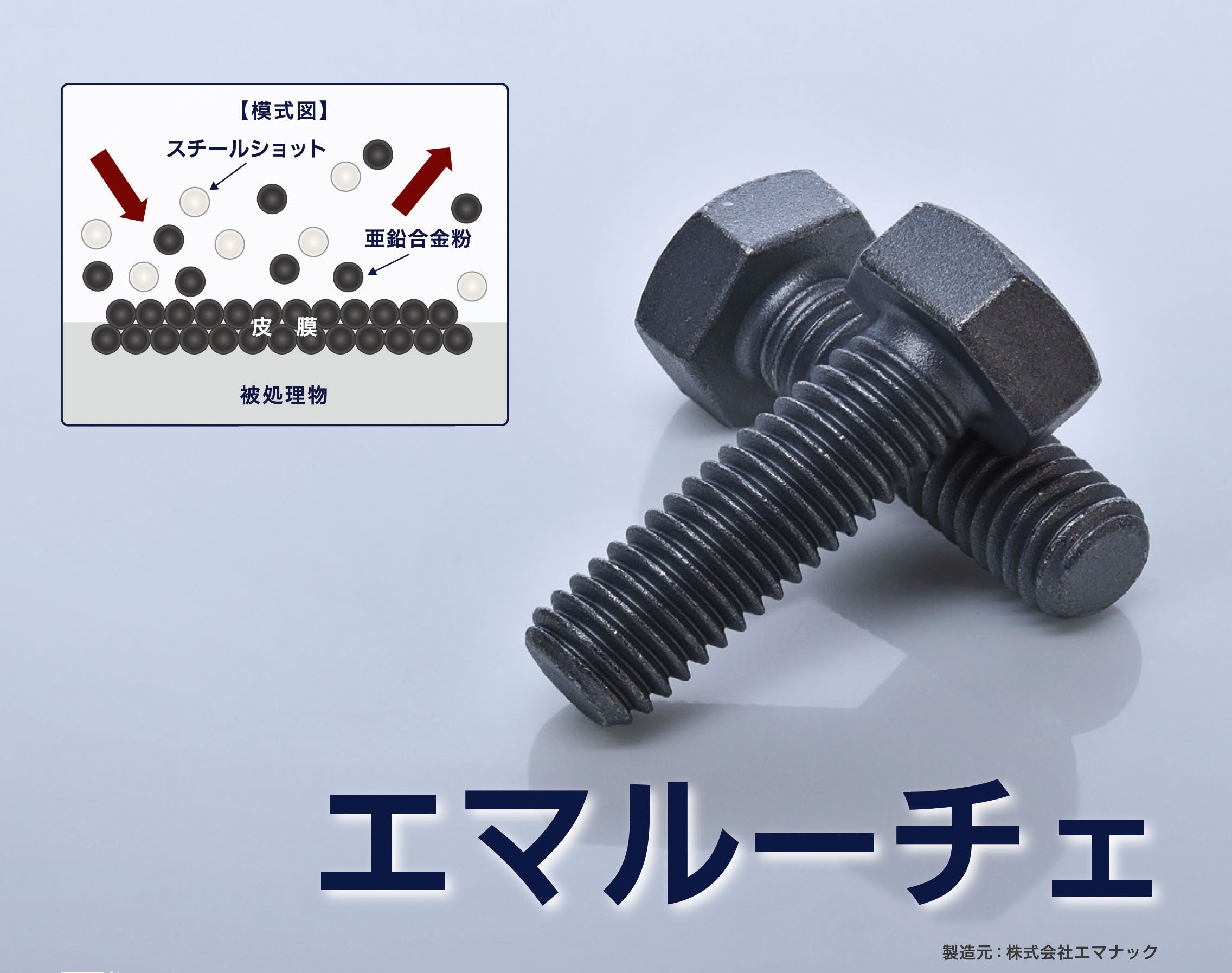
2つ目は、鉄の腐食対策技術として登場した「エマルーチェ」。こちらも、多くの製造現場で使用される代表的な素材だが、サビを防ぐためには、やはり加工が必要だ。「エマルーチェ」では、亜鉛を主にあらゆる金属を混ぜ合わせてつくった粉のような物質を高速で部品に吹き付けることで、表面に膜をつくり出すことができる。こちらもAlooHと同様、環境負荷の大きい溶剤を使用することなく腐食対策ができ、大幅な節電も可能となった。
また、「エマルーチェ」には、高い密着性もあり、加工後に部品を折り曲げることがあっても、メッキが剥がれてしまう心配は少ないそう。
今後の展開
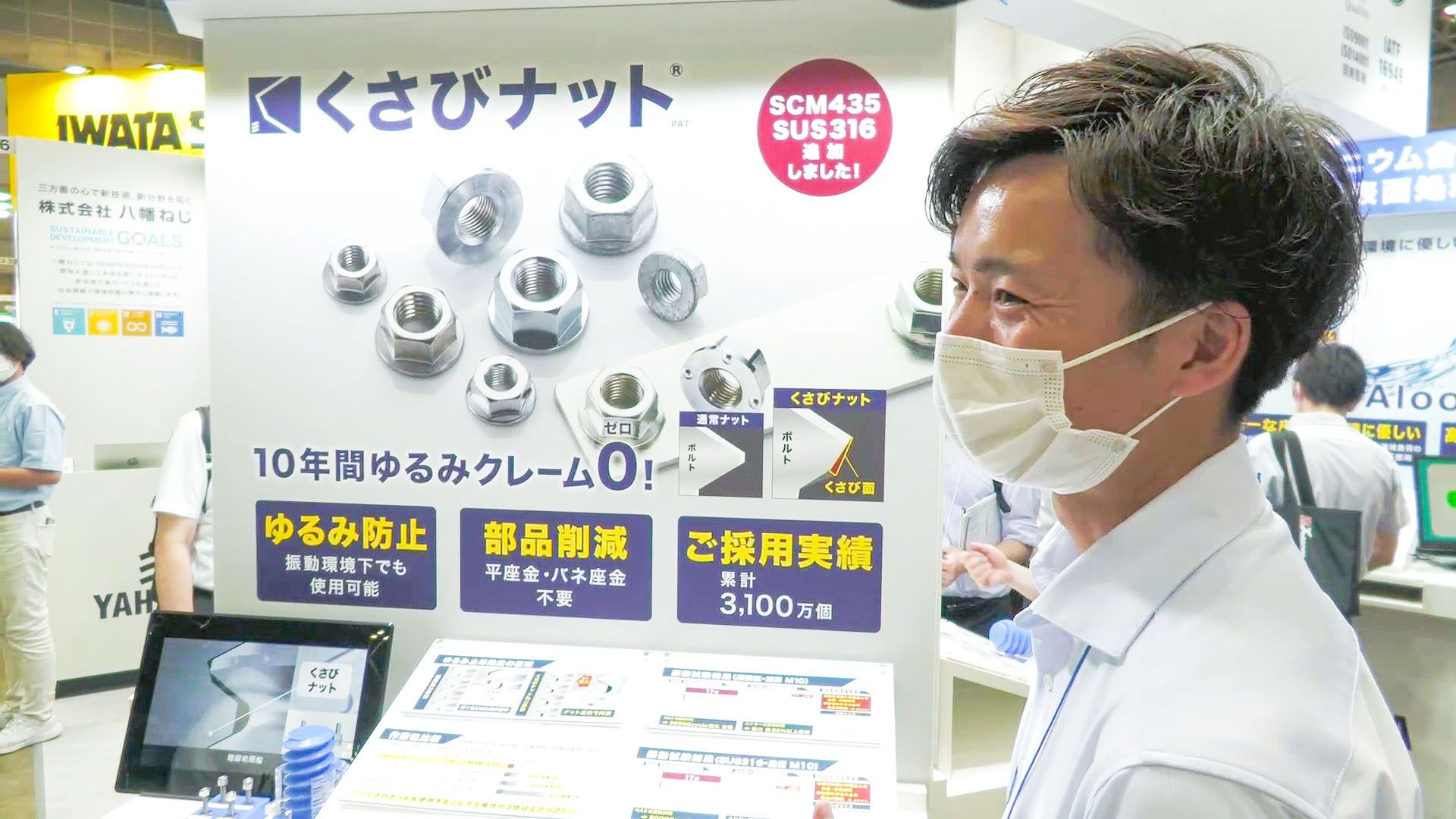
「1本1本は小さな存在である“ねじ”ですが、モノづくりには、欠かすことのできない大切な部品です。モノづくりの課題をねじで解決する。品質はもちろんのこと、現場の利便性向上や昨今あらゆる分野で求められているSDGs・カーボンニュートラルにも貢献していきたいと考えています。新技術をきちんと事業として成り立たせられるよう、現場に寄り添った商品開発と提案を行っていきたいです」と南関東営業所の水野 椋介所長は話す。
取材先:株式会社 八幡ねじ
URL:https://yht.co.jp
制作:工場タイムズ編集部